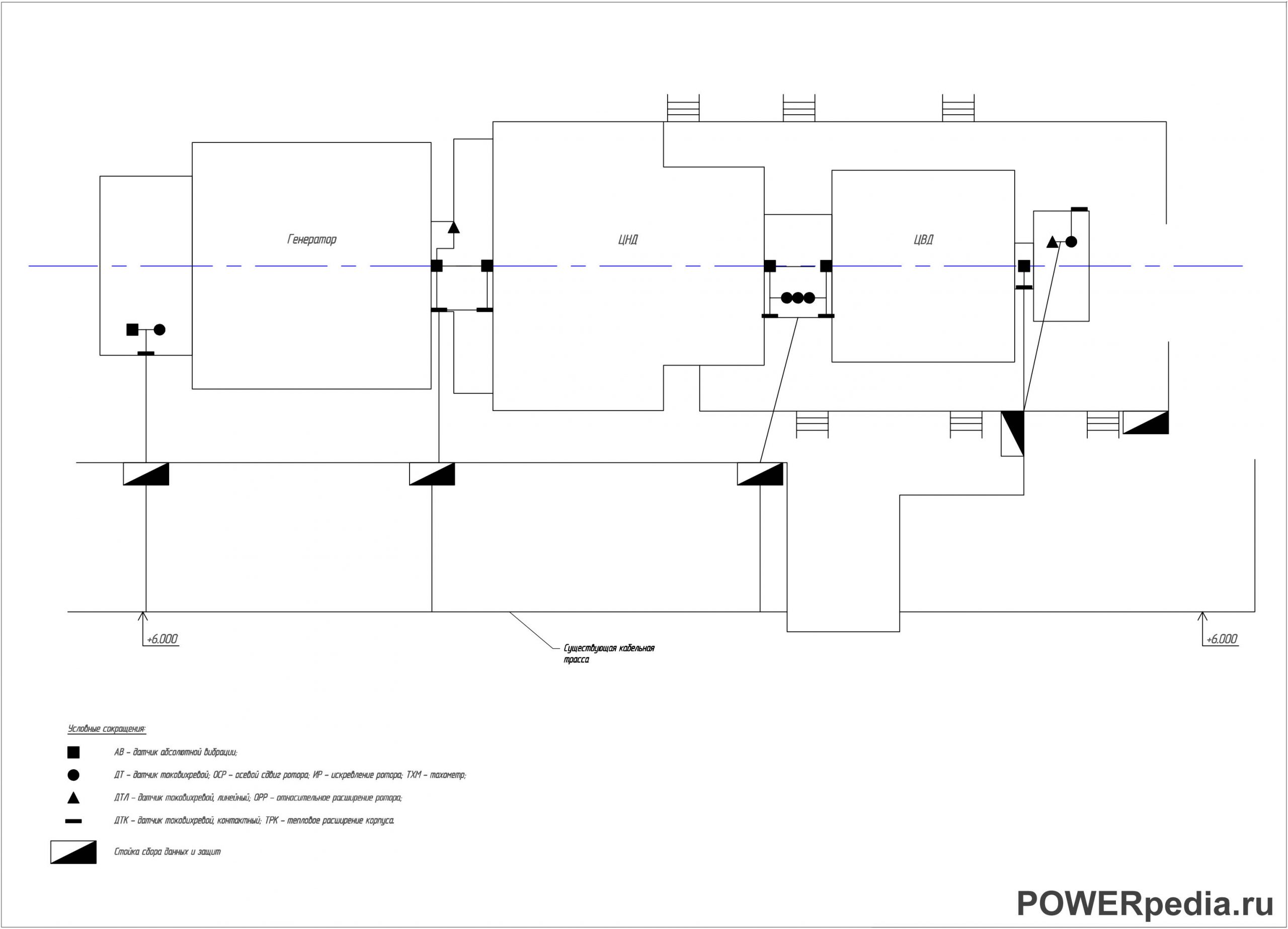
Cистема контроля, управления и диагностики турбоагрегата ПТ-65-130/13 на базе АСУ от НПП «Измерительные Технологии».
Назначение.
Система предназначена для:
— непрерывного контроля технологических параметров, вибрационного состояния и защиты турбогенератора в стационарных и переходных режимах работы путем измерения вибропараметров, скорости вращения, линейных смещений и искривления ротора;
— повышения безопасности эксплуатации технологического оборудования за счет получения оперативной и объективной информации о техническом состоянии турбоагрегата;
— снижения эксплуатационных расходов за счет предотвращения внеплановых и аварийных остановов агрегата;
— повышения культуры производства ремонтно-технических служб за счет внедрения современных средств мониторинга оборудования и информационных технологий.
Система выполняет следующие функции:
— непрерывный контроль состояния турбоагрегата по параметрам вибрации;
— непрерывный контроль смещения ротора;
— непрерывный контроль теплового расширения ротора ЦВД и ЦНД;
— непрерывный контроль теплового расширения корпуса турбины ЦВД и ЦНД;
— контроль выходной мощности генератора;
— непрерывный контроль скорости вращения вала;
— формирование управляющих сигналов для противоаварийной автоматики в случаях превышения параметров вибрации и осевого смещения ротора заданных предупредительных и аварийных уставок;
— оперативный диагностический контроль (мониторинг) по данным измерений абсолютной вибрации опор подшипников турбогенератора;
— формирование архива по всем измеряемым и вычисляемым параметрам (базы данных), просмотр и анализ архивных данных;
— анализ вибрационного состояния турбоагрегата на различных режимах работы (останов, валоповорот, набор оборотов, работа под нагрузкой, выбег).
Структура.
Система имеет три уровня иерархии. Нижний уровень — датчики и исполнительные механизмы, средний — модули системы ИТ-14, верхний — сервер сбора и обработки данных и операторская станция.
Связь между верхним и средним уровнем осуществляется по линии CAN. Сигналы, участвующие в защитах, от измерительных модулей до модулей защит проводят по выделенным линиям.
Датчики системы устанавливаются, как на поверхности конструктивных элементов турбогенератора так и внутри полостей картеров подшипников. По принципу работы датчики разделяются на пьезоэлектрические и вихретоковые. Индикатор оборотов ротора устанавливается на переднюю опору турбины.
Модули системы предназначены для согласования сигнала от датчика, предварительной обработке и передачи данных по лини CAN на оборудование верхнего уровня в цифровой форме. Модули для измерения поверхностной вибрации и осевого смещения ротора имеют дискретные выходы для модуля защиты, который формирует сигнал на останов турбины по алгоритму защит турбогенератора.
Персональные компьютеры верхнего уровня обеспечивают:
— приём и хранение полученных данных;
— визуализацию полученных данных и архивов;
— управление в пределах разграничения прав;
— анализ полученных данных для прогноза состояния турбины.