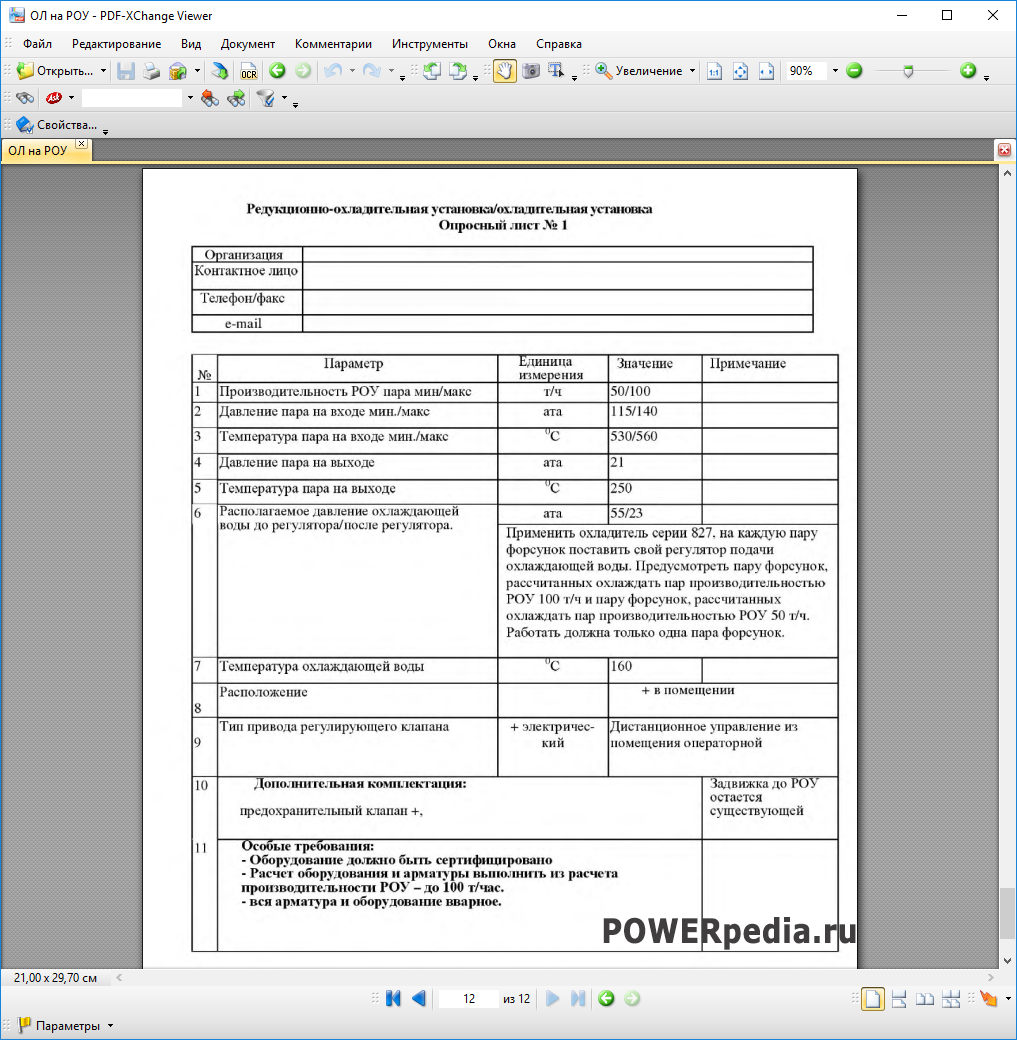
Энергетическая эффективность редукционно-охладительной установки (РОУ). В настоящее время на некоторых ТЭЦ существует возможность производить растопку котлоагрегатов через РОУ на коллектор 14 ата. Однако, в связи со сложившимся отпуском тепла в паре потребителям, низкими расходами пара на СН (особенно в летнее время), расходы пара на коллектор 14 ата малы для полной утилизации растопочного пара, который приходится во время растопки направлять в атмосферу, и при этом разгружать производственный отбор на работающей турбине. Поэтому решение использовать растопочный пар на параметры 21 ата, переведя его дополнительно на коллектор 21 ата при соответствующем давлении, приведет к экономии как тепловой энергии, так и конденсата, и позволит не снижать экономичность работающих турбоустановок.
Средний расход пара 21 ата потребителю составляет 60 т/час;
Среднее количество растопок за год — 26;
Экономия пара (конденсата) за одну растопку — 130 т;
Стоимость ХОВ — 87,95 руб./т.
Годовой экономический эффект от экономии конденсата:
Ихов=130*87,95*26=297,27 тыс. руб./год;
Экономия тепловой энергии при использовании растопочного пара составит — 104,9 Гкал за одну растопку.
При этом годовая экономия условного топлива составит:
Враст= 104,9* 152,134*26*10—3=413,93 тут/год;
Где:
bт=152,134 кг/Гкал — норматив удельного расхода условного топлива на отпуск тепловой энергии.
Дополнительная теплофикационная выработка электроэнергии за счет дозагрузки промышленного отбора турбоагрегатов в период растопки:
Эотб=130*(818-724)*0,8*26/860=295,55*10—3 кВт•ч/год;
Где:
1оп=818 ккал/кг — энтальпия свежего пара при Р=115 кгс/см2 и Т=525 °С;
1отб=724 ккал/кг — энтальпия пара производственного отбора турбины ПТ-65-130;
К=860 ккал/кВтч — физический эквивалент-постоянная применяемая при расчете выработки электроэнергии (Горшков А.С. «Технико-экономические показатели тепловых электростанций»-3-е изд., перераб. И доп. М.:Энергоатомиздат, 1984.-240 с., ил.);
П=0,8 — усредненный КПД проточной части турбины.
Повышение экономичности турбин при замещении конденсационной мощности теплофикационной составит:
Вцикл=295,55*(405,831 -267,324)* 10—3=40,94 тут/год;
Где:
bк=405,831 г/кВт•ч — плановый удельный расход условного топлива на отпуск электроэнергии в конденсационном режиме;
bт=267,324 г/кВт•ч — плановый удельный расход условного топлива на отпуск электроэнергии в теплофикационном режиме.
Суммарная годовая экономия топлива в результате реализации проекта
Вгод= Враст + Вцикл= 413,93+40,94=455,87 тут/год.
Перевести тут в стандартные виды топлива >>>
Сверху, на картинке, представлен опросный лист (ОЛ) на РОУ.